Selection of Research Topics
An important research theme within the Advanced Structures Group is using conventional materials in a smart way, by exploring and favourably combining geometry and pre-stress. The research topics below are a selection of past and present work that illustrate what we are working on. If you would like to know more, have a look at the publications or contact us.
Advanced Shell Structures
In recent years a lot of our work has focused on novel types of shell structures. By introducing a local texture pattern to thin-walled shells, it is possible to favourably change the global mechanical properties: textured shell structures. This may for example be used to introduce bending anisotropy to a previously isotropic material, which enables the design of bistable structures without using composite laminates.
A natural extension of this work led to morphing shell structures. These shells are capable of undergoing large changes in shape, whilst remaining within the material's elastic range. Indeed, these structures often display a strong mechanistic component, and can equally well be referred to as compliant shell mechanisms. The flexibility is obtained through corrugations and fold lines in the shell surface, which often leads to unexpected coupling between different deformation modes. These shells require a new modelling approach, which captures the hierarchical interactions between global kinematics and local shell deformations. Interestingly, many of these structures can change their apparent global Gaussian curvature, whilst undergoing only bending deformation at material level.
Examples include curved corrugated shells and folded shell structures. These folded sheets are either created using, or resemble, origami fold patterns. Here the purpose of the folding pattern is to impart both flexibility and stiffness to the material. It is the hierarchical combination of the opening and closing of the fold lines, and the developable deformations of the interlying material, that defines the mechanical properties of the shells.
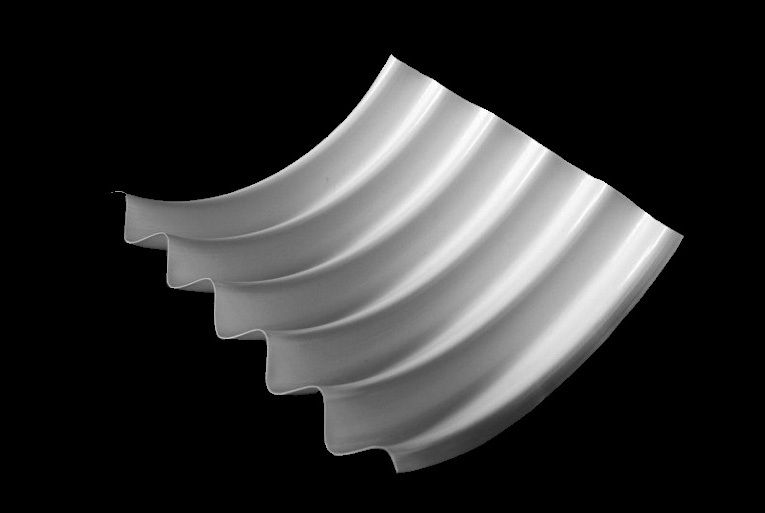
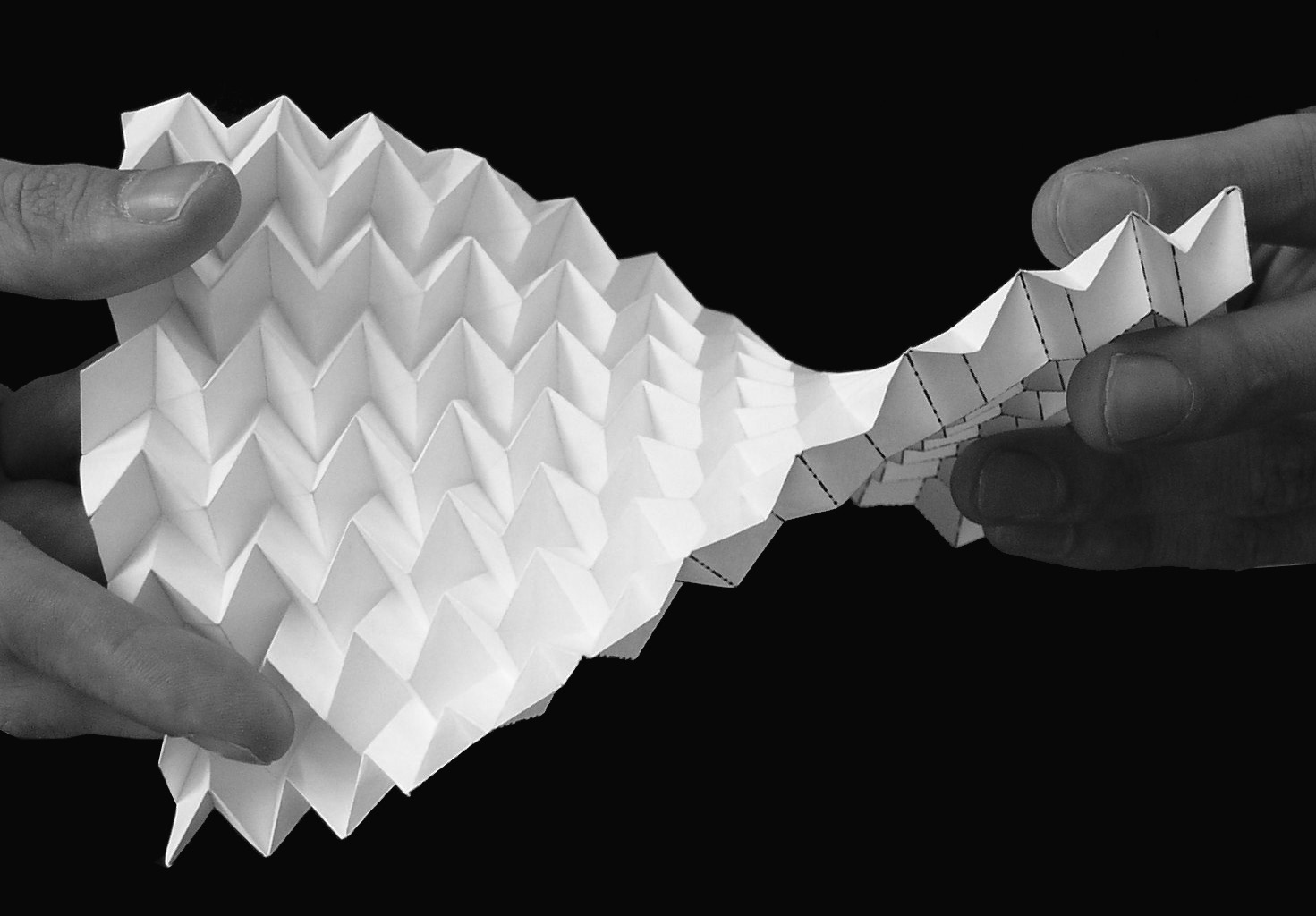
Surface Texture Through Buckling
Generating a surface texture in a shell can improve how the shell or structure interacts with the world around it. In the example below, a simple model of an airfoil section has a thin membrane wrapped around a solid core. The membrane is marginally wider than the core, and the wooden endplates can be moved axially in a controlled manner by turning the nuts. In one state, the surface is completely smooth; in the other, the endplates are compressing the membrane, which has clearly buckled. However, the core restricts both local buckling and the out-of-plane movement to such a degree that a regular buckle/wrinkle pattern forms over the entirety of the surface: notice how the size of the buckle facets are proportional to the radius of curvature of the section. Present testing of similar specimens in a wind tunnel indicates that switching on the texture, at the correct windspeed, can reduce the drag signficantly - as the dimples do on a golfball. But unlike a golfball, the surface can be switched to smooth again in order to yield better aerodyanmics at a different speeds. Other potential applications include "haptic" electronic displays, where the user experiences a tactile feedback, and building facades with tuneable reflection and absorption characteristics.
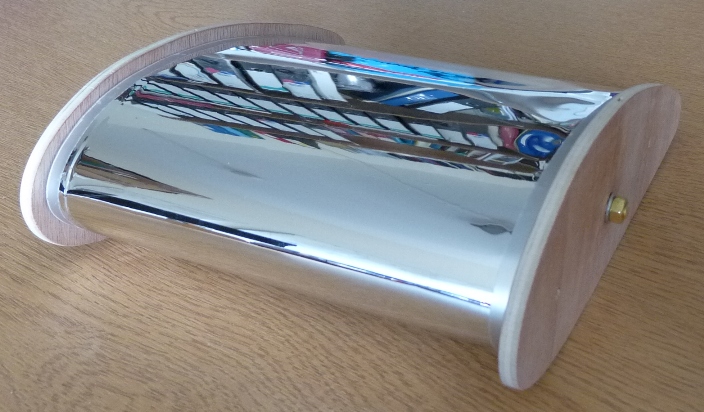
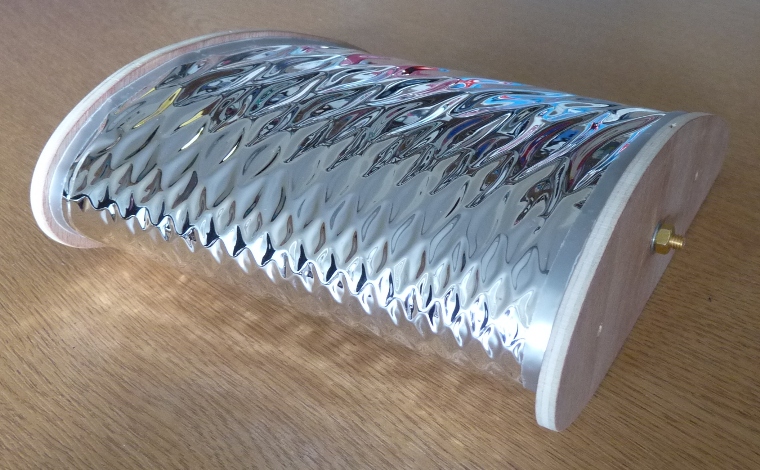
Multistable Structures
Unlike conventional structures, multistable structures have more than one stable state, and can move elastically (and thereby repeatedly) from one state to another. This behaviour can be achieved through combinations of pre-stress, anisotropic material and geometry. This multistable behaviour is of great interest as it enables the structure to attain different shapes, with actuation energy only required to move from one shape to the other. This property is useful for deployable structures, where the structure is then stable in its compact form, and once again stable in its fully deployed state.
Examples include the Rolatube mast, bistable corrugated sheets used for roll-up computer screens, and multistable dimpled sheets as adaptive skins for aircraft wings. Even nature employs the idea of bistability, for example in the Venus Fly trap - one of the fastest movers in the plant kingdom.
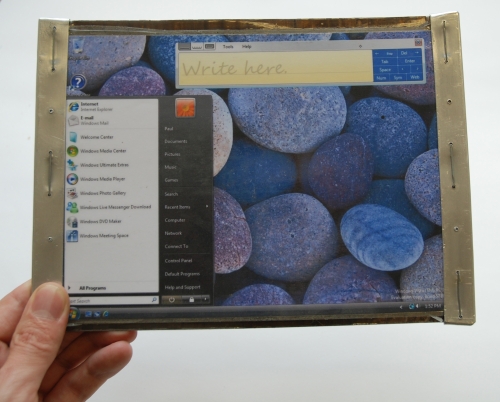
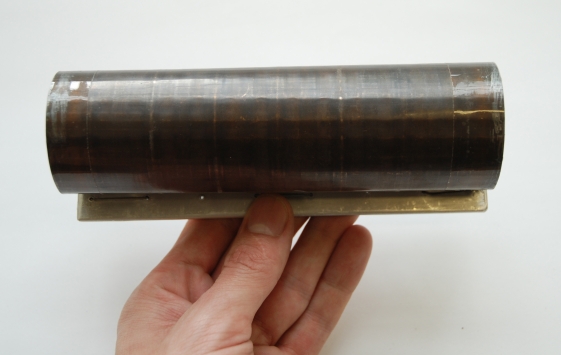
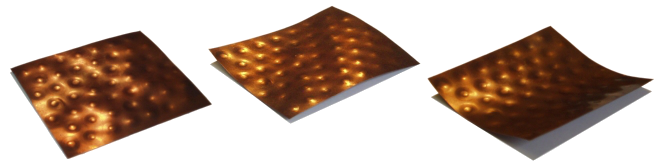
Deployable Structures
A wide range of structures can benefit from being transported in a compact form, and then deployed to its full extent when needed. Examples range from the mundane umbrella, to advanced solar panel arrays for space applications. The structures group has a rich heritage in the development of deployable structures, which the Advanced Structures Group continues.
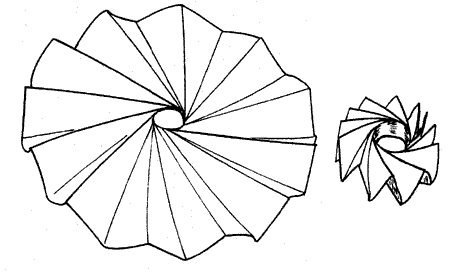
In early 2012, the Advanced Structures Group started work on DeployTech, a large collaborative project to design deployable space structures. In collaboration with Surrey Space Centre and several European partners we work to design an inflatable satellite de-orbiting device.
Tensegrity Structures
Tensegrities are pre-stressed pin-jointed frameworks, where the tension members are replaced by cables. Their analysis provides interesting insight into the stability of prestressed trusses, as well as a fruitful field of application of symmetry analysis.
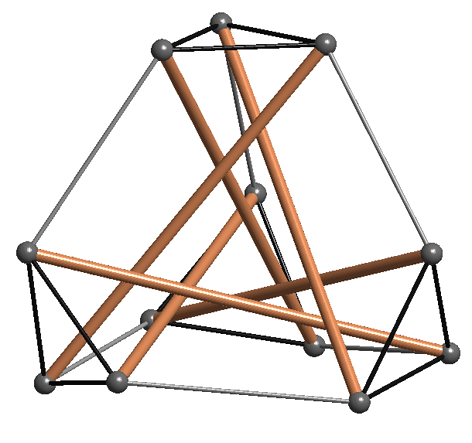
Zero Stiffness Structures
Structures that exhibit zero stiffness can change configuration without any force; in other words, they are in continuous equilibrium. Unlike mechanisms, however, components of the structure will undergo elastic deformation. The stresses, however, are balanced to create a constant total potential energy, thereby yielding zero stiffness deformations. A classic example of a zero stiffness mechanism is an Anglepoise lamp, but this field has been extended in recent years to cover zero stiffness tensegrity structures, zero-stiffness shells, and constant force cantilevers.
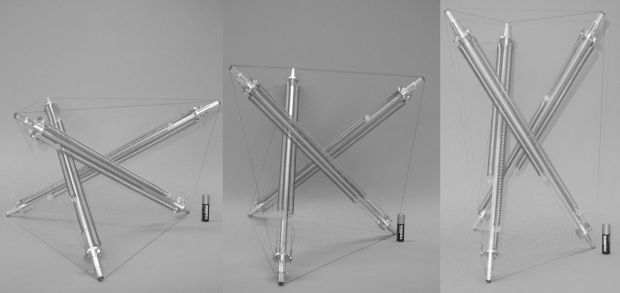